Front Loader Inspections - Workplace Inspection Checklists
The construction industry has seen an average of 36 fatalities per year to workers over the past 5 years.
In addition there have been nine fatalities in the past five years involving front loader buckets within the waste and recycling sector.
Front loaders (also often referenced as a bucket loader, front-end loader, payloader, high lift, scoop, shovel, skip loader, wheel loader, loading shovel, or skid-steer) are versatile machines, widely used in the waste and recycling, and construction sector. However, driver visibility can be affected by various blind spots caused by the bucket (and load), the engine at the rear and the cab pillars. These can significantly reduce the driver’s ability to see pedestrians and, to a lesser extent, other vehicles.
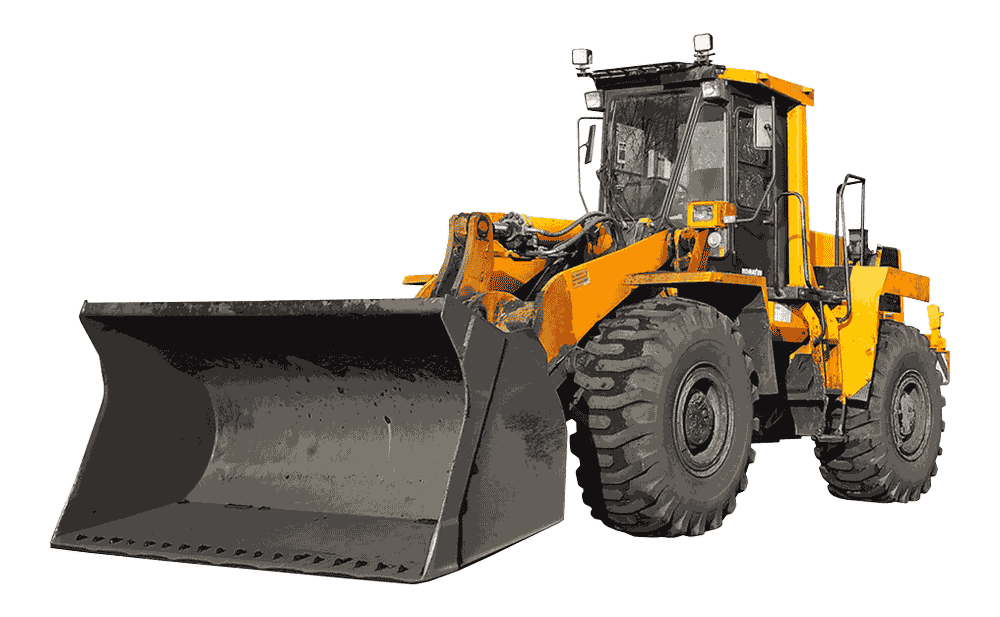
Regulation 4 of The Provision and Use of Work Equipment Regulations 1998 (PUWER) requires machinery to be suitable for the purpose it is used for. This also applies if the equipment is adapted, eg by fitting a larger bucket.
Before using wheeled loaders (or making changes to them), you should review your workplace transport risk assessments to ensure they will be safe to use in your environment and in the way that you intend to use them.
Don’t assume your vehicle comes supplied with the most appropriate or comprehensive mirrors etc for your specific needs (this is particularly important with second-hand machines). Critically assess the visibility and consider fitting additional mirrors, cameras etc if necessary.
When fitting items of interchangeable equipment, such as larger capacity buckets, ensure the modified machine meets essential health and safety requirements (EHSRs) of the Supply of Machinery (Safety) Regulations. You should do this by consulting with the manufacturer of the interchangeable equipment or the base machine manufacturer.
Where modifications reduce forward visibility, consider what additional aids can be fitted to help the driver and what additional risk controls can be implemented to protect pedestrians.
If you fit oversized buckets, you should be able to demonstrate that the risks are adequately controlled through your risk assessment. Daily checks of mirrors and other safety features are vital – if they are damaged or broken, the vehicle should not be used.
The effective maintenance of a front loader is an essential part of safe operation. As with all machines a loader wears, deteriorates and can suffer damage over time. The maintenance process (including checks and inspections) monitors, prevents and rectifies this deterioration. It is important that the personnel asked to carry out these tasks have the necessary machine-specific training, experience and competence in both periodic and breakdown maintenance.
Both the user and owner of the wheeled loader have a responsibility to ensure that they are maintained in a safe working condition.
Basic checks and inspections should be carried out in accordance with company instructions and the manufacturer's recommendations:
• Daily/Pre-use Checks - these are carried out prior to each use of the machine and include checks for damage and correct functioning of the loader;
• Shutdown Checks - these are carried out at the end of each shift and are an opportunity to report defects which may have developed during the shift;
It is the responsibility of the site management to ensure that all front-end loaders are adequately maintained in efficient working order and in a state of good repair.
A scheduled preventative maintenance program helps to meet these requirements. The frequency at which the maintenance activities are carried out must consider the machine usage and the working environment. A record of maintenance should be kept for each loader truck.
Comprehensive maintenance records are essential to the safe, efficient and economical operation of a truck. They provide a complete “cradle to grave” history of the individual machine giving the following benefits:
• evidence of adequate maintenance as part of the management system;
• establishing breakdown trends over time and providing information for the review of maintenance frequency;
• identification of component failure trends for feedback to the manufacturer;
• evidence of adequate maintenance to the Enforcing Authorities in the event of an incident;
• enabling the performance of the bucket truck to be reviewed over time to inform future purchases.
Good to Go Safety provides the perfect solution by allowing comprehensive checks to be completed, using our loader truck checklists, with a duplicate copy retained for management records. If faults are found then the status tag can be updated to clearly display a “Do Not Use” message until the truck has been repaired and deemed safe to use.
Front Loader Inspection Books - 25 Checklists
Front loader inspections help spot potential faults before they develop into a more serious and cost..
£6.20
Front Loader Inspections - Weekly Checklist Kit
Loader bucket trucks (also known as shovel loaders or front loaders) have the capacity to cause seri..
£37.10
Front Loader Inspections - Daily Checklist Kit
Loader bucket trucks (also known as shovel loaders or front loaders) have the capacity to cause seri..
£109.50
Front Loader Poster - Visual Inspection Checklist
Our front loader (shovel loader) poster has been designed to highlight key components of front loade..
£21.77
Inspection Information Station
The information station will provide your workplace with the ideal central location to store inspect..
£233.20
Inspection Wallet and Pen
A handy wallet that not only provides additional protection from the elements but also gives inspect..
£6.20
Weather Resistant Inspection Holder
These industrial strength pockets have a press seal fastening to keep important documents clean and ..
£6.31