Equipment Inspection Safety Videos
Inspect all your workplace equipment on your mobile
A quick overview of some of the features that TakeAIM can offer businesses. Set up an account today and take charge of all your workplace equipment - no matter how unusual they are.
TakeAIM helps companies analyse equipment and spot re-occurring issues to help you resolve them before they happen again. This will help you manage and reduce maintenance downtime whilst ensuring you comply with PUWER and other major legislative bodies.

The importance of pre-drive checks
Before setting off in the car, taking time to check over the vehicle to ensure there are no obvious defects can dramatically improve the safety for your self and others on the road. Using the TakeAIM app to complete and record these inspections provide a great tool for any fleet manager and gives them real-time visibility of all completed checklists.

Inspections and maintenance for EVERY asset at work
The TakeAIM app includes a wide range of pre-installed equipment checks - ready to use and you can also create your own at no additional cost. So whatever your industry and whatever your equipment you can now monitor, manage and record your maintenance program from the palm of your hand.

TakeAIM Now Available to Download
We’re now on the next chapter of Good to Go Safety’s story by introducing TakeAIM, the digital version of our award winning tagging and checklist system. We believe that our customers will be extremely pleased with TakeAIM as it makes our inspections even more useful and accessible than ever before.

Good to Go Safety is going digital with a new app called TakeAIM.
TakeAIM is an auditing, equipment inspection and maintenance app used to help companies manage workplace equipment. Combined with a web platform, TakeAIM provides visibility and insights to help reduce maintenance down time and improve safety. Your team can inspect all assets, identify quarantined equipment and communicate issues directly to their head office. Helping managers analyse equipment and spot re-occurring issues to help resolve them before they happen in the future.
Good to Go Safety - Dec 5, 2018

We believe that keeping your business moving is critical.
Bob a Health and Safety Manager and Bill the Managing Director have a chat regarding their company's current Forklift Management programme and what Bob requires to not only make life easier, but also to comply with legal obligations under PUWER and show that they support and look out for their employees.
Any loss in productivity can prove costly, not just financially: The cost of unplanned maintenance includes lost production; higher costs for parts and shipping; as well as time lost responding to emergencies and diagnosing faults while equipment is not working; not to mention the impact on your reputation following delayed deliveries.
Good to Go Safety - Nov 14, 2017

Visual Inspections
Our award winning equipment tagging and checklist systems can help you to keep your workplace safe, reduce repair costs and comply with legislation.
The system is only ever as good as strong as the weakest link – if one small cog in the machine fails, it can bring the whole system to a stop. Complacency, uncertainty or simply having an ‘off day’ could lead to the inspector becoming that weak link.
Providing visual reminders can strengthen the Good to Go Safety system and that’s why we’ve developed a range of posters. The posters compliment the checklists with their eye-catching design and provide additional details as to what should be checked.
Good to Go Safety - Feb 16, 2017

Proactive vs Reactive Forklift Maintenance
Unplanned, reactive maintenance has many overhead costs that can be avoided when implementing our equipment maintenance system. That's why forklift maintenance is vital to ensuring you are always Good to Go!
Good to Go Safety- Jan 5, 2017

A staggering 33% of all crane accidents (due to poor maintenance) result in a fatality.
Overhead cranes are subjected to immense forces, parts such as hoists and cables will see inevitable wear and tear; especially when exposed to extreme heat and/or chemicals. Failure can have very serious consequences for any plant, building structure or personnel in the area.
Over half of all crane incidents involve a dropped load, an estimated 60% of which could be attributed to poor crane maintenance and 15% to the failure of wire ropes/cables.
Good to Go Safety - Sept 5, 2016

If you have a forklift basket on site then now’s the time to introduce Good to Go Safety inspections to your workplace equipment.
We were asked to produce a checklist for forklift work platforms (also referred to as a man basket or safety cage) and so we’ve developed a comprehensive inspection programme to suit their needs and help them meet their PUWER and LOLER obligations. With so many of our customers working within warehousing and construction industries we know the demand for this latest checklist will be high and pre-orders have already began to leave our own warehouse.
Good to Go Safety - Aug 4, 2016

Tractor Inspection Checklists
Farming accounts for more than 30 deaths and over 1000 serious injuries every year in the UK. Keeping an audit of when inspections have been carried out and what work has been done on farming equipment is very important.
These records help show that equipment is well maintained and regularly checked, providing invaluable evidence in the event of an accident. Comply with HSWA, PUWER, Road Traffic Act, LOLER & HSE regulations
Good to Go Safety - May 23, 2016
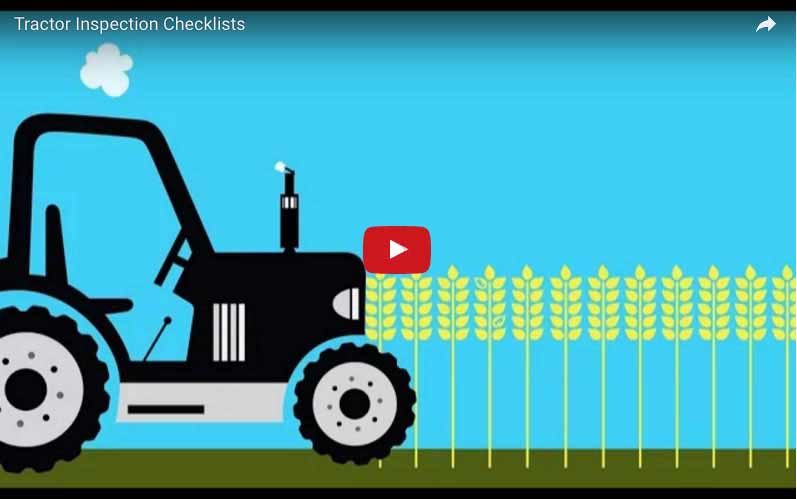
How our Tag is Made
Our Universal Status Tag has come a long way from its initial concept on the back of an old paracetamol packet to the current finished article. Whilst designing our tag we knew that we'd need it to withstand the everyday bumps and scrapes of working life, that's why we manufactured it from tough, durable polypropylene.
Customer feedback, increasing sales and winning awards all let us know that we've designed an impressive product and we continue to develop and add new checklists to our range. Behind the scenes we are constantly looking for further improvements and enhancements so watch this space! To find out how our universal status tag is made - watch our 20 second video.
Good to Go Safety - May 6, 2016
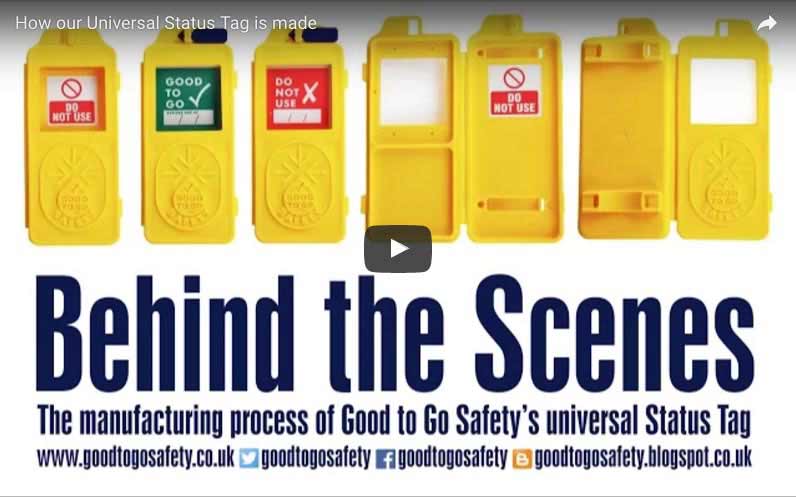
Forklift Inspection Checklists
We believe that keeping your business moving is critical. Any loss in productivity can prove costly, not just financially: The cost of unplanned maintenance includes lost production; higher costs for parts and shipping; as well as time lost responding to emergencies and diagnosing faults while equipment is not working; not to mention the impact on your reputation following delayed deliveries.
Unplanned, reactive maintenance has many overhead costs that can be avoided when implementing our equipment maintenance system. That's why forklift maintenance is vital to ensuring you are always Good to Go!
Good to Go Safety - May 27, 2016
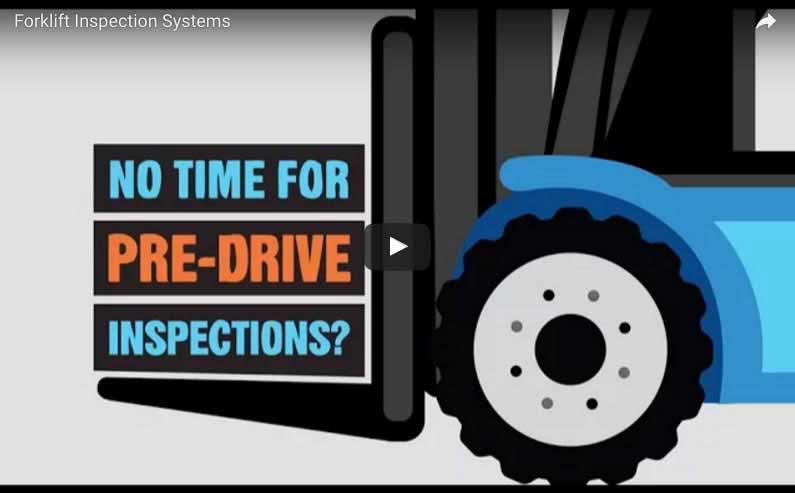
Ladder and the Faulty Ladder
Ladders account for about 33 percent of all fall from height accidents in the workplace, many of which could have been avoided with training, guidance and safety maintenance. All ladders should be checked prior to use for any faults or general wear and tear.
Our innovative tagging and inspection system ensures essential pre-use inspections are carried out. Helping reduce the risk of any accident like Bob's. Good to Go Safety helps companies to improve safety, reduce maintenance costs and comply with legislation.
Good to Go Safety - Mar 3, 2016
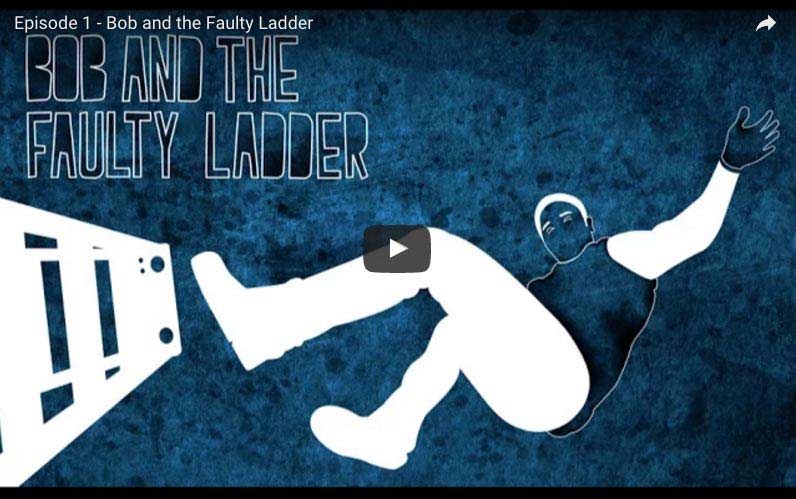
Return of the Bob
After his ladder accident, Bob returns to work with a new respect for equipment safety. With his new insight, he is dedicated to ensuring no one else is injured due to equipment negligence, but even the best of intentions can fall short without clear protocols in place.
Every year approximately 2,000 accidents and 10 fatalities are reported as a result of forklift operation in the UK. That's around 40 serious injuries every week!
Good to Go Safety offers a simple, effective and affordable solution to forklift safety and provides a flexible solution which can be adapted to meet your company requirements. The system has three main parts, a Tag, Check Book and Tamper Evident Seal.
Good to Go Safety - Mar 9, 2016
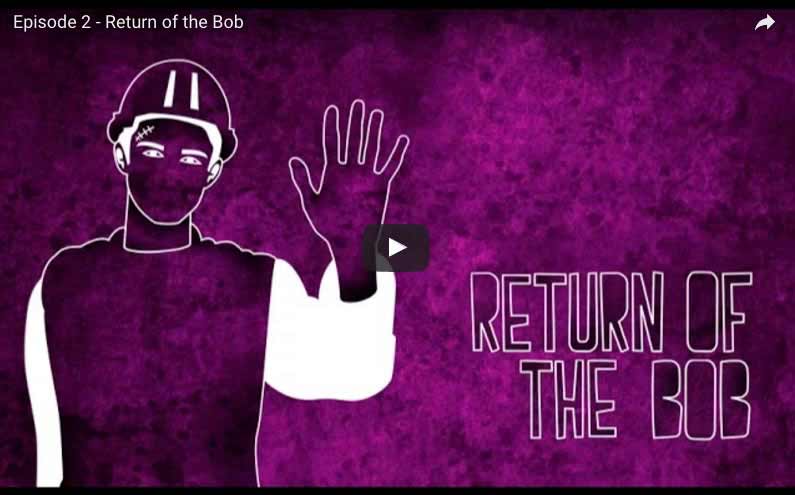
Be Like Bob
After Bill's accident, management introduce a new safety regime and appoint Bob as safety manager.
Bob introduces us to the new safety regime and goes through the steps to ensure that equipment is in good working order so that no one can be injured on his watch again.
Good to Go Safety - Apr 7, 2016
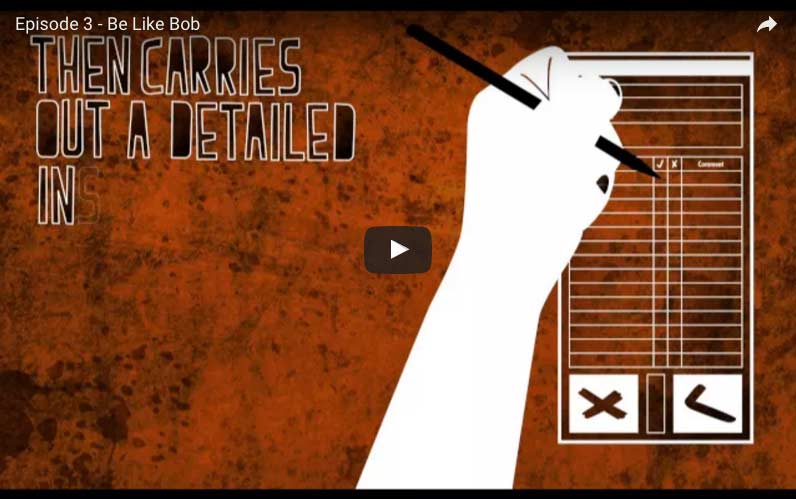
Warehouses
Remove the danger of assumptions, reduce maintenance costs, comply with legislation, improve workplace safety and communicate equipment status with Good to Go Safety
Our innovative tagging and checklist system helps increase workplace safety plus much more. It ensures employees know when a forklift, ladder, scaffold tower, scaffolding, trailer, pallet racking plus so many other types of equipment have been checked and an inspection has been completed.
It is a perfect addition to your Health & Safety maintenance and equipment management programmes - ensuring equipment and employees are always Good to Go!
Good to Go Safety - Feb 23, 2016
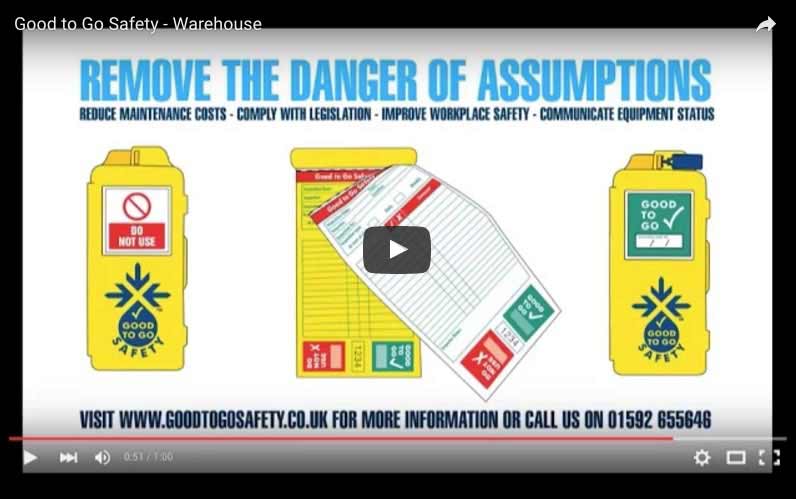
Spotting Faults
Good to Go Safety is a Safe Equipment Management System (SEMS), which encourages a safety inspection on workplace equipment and is the ideal addition to your H&S, maintenance and equipment management programmes.
Suitable for Forklift, Ladder, Scaffold, Scaffolding, MEWP, Harness, Fleet Vehicles, Trailers, Podium Steps, Pallet Trucks, Racking and more.
Watch this short video to find out how simple the system is to use.
Good to Go Safety - Dec 18, 2015
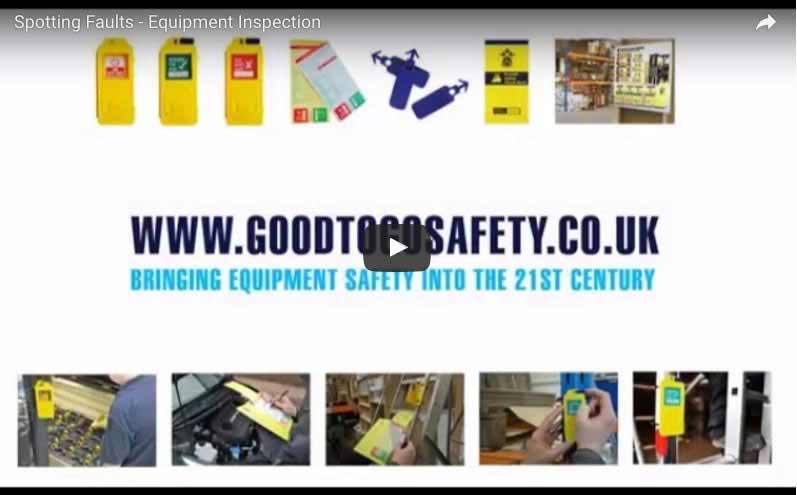
The Danger of Assumptions
It is easy to get complacent when it comes to equipment safety.
If an employee uses the same equipment every day (e.g forklift/ladder/vehicle etc) without carrying out routine checks it is easy for them to fall into the trap of assuming that “it was fine yesterday even though it made a few odd noises, I’m sure it will be fine today”.
Each day that this assumption continues to be made, so the false feeling of security grows, until the equipment in question fails.
Good to Go Safety - Nov 27, 2015
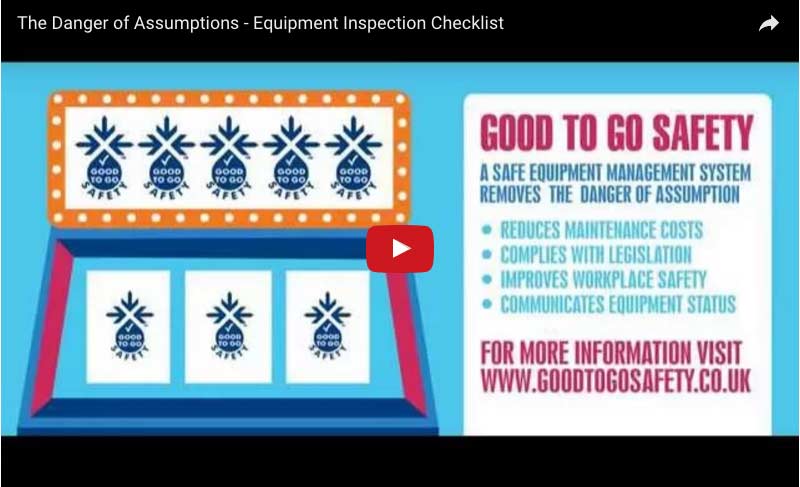
A detailed overview of the Good to Go Safety system. An innovative range of inspection & tagging systems for ladders, scaffold, forklifts, racking, MEWPs, harnesses, fleet vehicles, podium steps and specialist equipment. Helps to prevent accidents; comply with legislation; provide a record of inspections; quarantine faulty equipment; reduce maintenance costs & empower employees. Easy to use, easy to implement and easily affordable.