Harness Inspections - Workplace Inspection Checklists
A harness is among the mainstays for fall protection
Working at heights is an expected part of the construction industry, along with the understanding that the higher the height, the higher the risk.
Defects can go undetected without a suitable inspection regime being in place. Equipment can fail, and without regular inspection and maintenance procedures, items of equipment can have faults that remain undetected for pro-longed periods of time. This may result in an increased risk of injury or harm to technicians, plant and/or equipment. Despite inspection and maintenance procedures, technicians should remain vigilant through pre-use checks (often referred to as “buddy checks”) and conduct pre-use function tests for all load-bearing equipment before using it. In addition, ongoing monitoring is required to detect damage that may have occurred during use.
.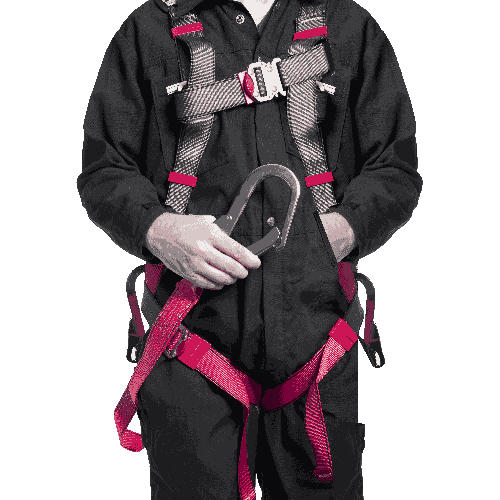
Inspection of work equipment & PPE plays a vital role in protecting the safety of the technicians who use it. It is important in ensuring the continued safety of those using life supporting equipment. Correct and thorough inspection also ensures that organisations are compliant and not left open to litigation. There should never be any doubt about the continued serviceability of an item of equipment.
Things can go wrong when procedures are not in place, are incomplete or are not followed. The opportunity is missed to identify actual or potential defects. Complacency can also result in defects being overlooked. We would recommend reading IRATA’s International code of practice for industrial rope access which can be downloaded: click here for more information, with particular reference to section 2.10 (Inspection, care and maintenance of equipment) and Annex H relating to Inspection of equipment.
Equipment inspections generally fall into three categories:
• pre-use check; These must be carried out by rope access technicians on their own equipment before first use each day. It is advisable to monitor the condition of equipment through the duration of the task, to ensure no damage or intervention has prevented equipment or systems from functioning correctly.
• detailed (‘thorough’) inspection; These are formal inspections and they must be carried out: 1. before first use; 2. upon receiving an item from a third party; 3. every 6 months (or at intervals specified in an inspection scheme drawn up by a competent person).
• interim inspection; These should be carried out where a risk assessment has identified the potential for high wear and tear or other dangers in the period between detailed inspections, e.g. following an incident, use in a hazardous environment, potential overload, etc.
All equipment manufactured from man-made fibres, e.g. ropes; webbing; harnesses; lanyards, should be chosen, used and inspected with particular care as it is susceptible to varying types and amount of damage, some of it not very easy to identify.
Inspection of the harness should consist of both a visual and tactile check and the Good to Go Safety Harness Checklist covers essential components to help ensure the harness is safe to use. WAHR (The Work at Height Regulations) stipulates the need for records to be kept of all completed checklists, each checklist copy should be kept on site until work is completed and stored for a further 3 months off site.
If possible we recommend that harnesses are stored in lockers or kit bags and that a status tag is attached to that (rather than the harness itself). We suggest this to avoid covering any of the webbing on the harness with the tag and the potential to miss potential damage. The tag can be used to display the current checklist and will indicate the current status and date of inspection, whilst a duplicate of the completed checklist is retained inside the check book for management records.
Useful downloads can be found in Legislation & Regulation. BS EN 365:2004 and BS 8437 also contain information on periodic safety inspection of fall protection.
Universal Status Tag
Designed by experts in the equipment inspection field, The Good to Go Safety Status Tag attaches to ..
£8.40
Harness Inspection Books - 25 Checklists
Carry out pre-use checks and spot potential faults before they develop into a more serious and costl..
£6.20
Harness Inspections - Weekly Checklist Kit
Carry out pre-use checks and spot potential faults before they develop into a more serious and costl..
£37.10
Harness Inspections - Daily Checklist Kit
Carry out pre-use checks and spot potential faults before they develop into a more serious and costl..
£109.50
Harness Poster - Visual Inspection Checklist
Our harness safety poster has been designed to highlight key components of a harness and reinforces ..
£21.77
Inspection Information Station
The information station will provide your workplace with the ideal central location to store inspect..
£233.20
Inspection Wallet and Pen
A handy wallet that not only provides additional protection from the elements but also gives inspect..
£6.20
Inspection Book Dispenser
Allow the storage of checklists in a central location for quick and easy access to important inspect..
£13.25