Telehandler Inspections - Workplace Inspection Checklists
The unsafe use of Telehandlers has led to a significant number of serious accidents, tragically including some fatalities.
Telehandlers (also known as Rough Terrain Telescopic Handlers or Variable Reach Trucks) make a valuable contribution to the construction process by enabling materials to be unloaded from delivery vehicles, transported around construction sites and placed at height (reach).
They are versatile machines which can be fitted with a wide range of attachments such as buckets, skips, work platforms and crane jibs. Unfortunately there have been a significant number of accidents involving the use of telehandlers, which have tragically included a number of fatalities. An effective and safe telehandler is one which is well matched to the type and size of load to be carried and lifted, together with the environment in which it is to be used. Attachments for use with telehandlers should be chosen with care to ensure that the combination of telehandler and attachment is both safe and productive. It is essential that all attachments are compatible with the telehandler with which they are to be used.
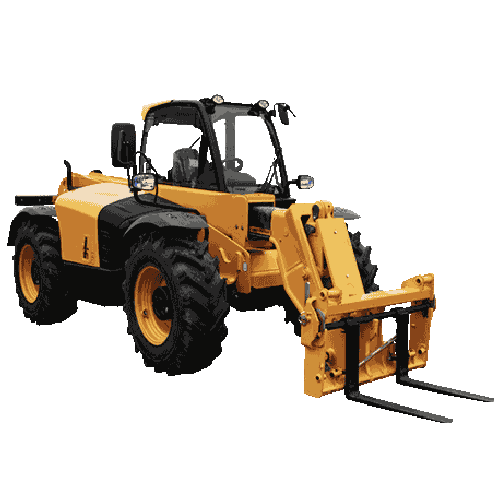
It is important that the use of telehandlers is subject to regular review and constant monitoring to ensure that tasks are being carried out as planned, that supervisors and operators have the necessary competences and that planning is effective. The effective maintenance of a telehandler is an essential part of safe operation. As with all machines, a telehandler will wear, deteriorate and can suffer damage over time. The maintenance process, including checks and inspections, monitors, prevents and rectifies this deterioration. It is important that the personnel asked to carry out these tasks have the necessary machine-specific training, experience and competence in both periodic and breakdown maintenance.
Telehandlers require the manufacturer’s preventative maintenance instructions to be strictly complied with, if safety is to be maintained in use. Checks and inspections should be carried out taking account of the frequency of use of the telehandler and the environmental conditions in which it works. Both the user and owner of the telehandler, and any attachments used with it, have a responsibility to ensure that they are maintained in a safe working condition. In practice the maintenance, other than pre-use checks, is normally undertaken by the telehandler owner on behalf of the user.
In addition to pre-op walk around checks the Lifting Operations and Lifting Equipment Regulations 1998 (LOLER) require that all lifting equipment is thoroughly examined by a competent person at specified intervals:
1. When the telehandler is put into service for the first time (LOLER Reg. 9(1))
2. A period not exceeding 12 months if the telehandler is only used for lifting goods (LOLER Reg. 9(3)(a)(ii));
3. A period not exceeding 6 months if the telehandler is used for lifting persons (LOLER Reg. 9(3)(a)(i));
4. After any major alteration or damage (event) (LOLER Reg. 9(3)(a)(iv))
Assuming the risk of deterioration is present with any equipment, the importance of pre-use checks to identify any day-to-day damage, faults or failure cannot be underestimated. The Good to Go Safety Telehandler inspection checklist system is flexible, allowing pre-shift start, daily, weekly, monthly or annual checks to be implemented – every site is likely to have differing requirements and the Good to Go system can be adopted to suit those needs. Written records of completed straddle truck inspections are retained as part of an audit trail, and any equipment that fails an inspection can be withdrawn from service for repair or maintenance with a “Do Not Use” message displayed in the tag for all to see until such time that repairs are completed. Placing the status tag at the entry point to the vehicle helps maximise visibility to all potential users and once the completed checklist is placed inside the tag it will clearly state the status and date of the last inspection, helping remove the risk of assuming that someone has already carried out the checks by clearly displaying if it has been completed.
LOLER also requires that lifting accessories and lifting attachments are thoroughly examined at intervals not exceeding six months (LOLER Reg. 9(3)(a)(i)).
Operators of the telehandler should undertake daily and weekly checks as safe system of work / manufacturers’ recommendations and records. They should advise their supervisor of any faults found on the equipment. The supervisor should check regularly (maximum of weekly intervals) that the operator is carrying out their daily and weekly checks. Once operations commence, the contractor / principal contractor should undertake random sample checks off equipment documentation / inspection/ maintenance records.
Telehandlers require the manufacturer’s preventative maintenance instructions to be strictly complied with, if safety is to be maintained in use. Checks and inspections should be carried out taking account of the frequency of use of the telehandler and the environmental conditions in which it regularly works. If the operator is considered to be competent to carry out routine pre-use and weekly checks, they may be authorised to do so. The employer of the person carrying out these checks should ensure that the machine is taken out of use for the period of time required to carry them out. Also, the employer or authorized person carrying out the checks should ensure that a safe system of work is in place to prevent personnel from being exposed to risk, for example from the inadvertent operation of the equipment.
Basic checks and inspections should be carried out in accordance with company instructions and the manufacturer's recommendations: • Daily Pre-use Checks - these are carried out at the start of every shift (or day) and include checks for damage and correct functioning of the telehandler • Weekly Inspections - these are additional inspections to the pre-use checks.
These checks and inspections should be recorded If there is a defect that affects the safe operation of the telehandler it must be reported and the machine taken out of service immediately. If it does not affect the immediate safe operation of the telehandler the defect should be reported to the supervisor so that repairs may be carried out in a timely manner. There must be provision for the operator(s) of telehandlers to make written reports of defects or observations immediately they are identified.
The Good to Go Safety telehandler checklist will help you to comply with much of the above, enabling pre-use checks of critical components to be completed. Upon completion of the telehandler inspection checklist, the top copy can removed, folded and places inside a Good to Go Safety status tag to display the date and findings of the latest checks, whilst a duplicate copy is retained and recorded inside the book, which can be made available to the supervisor or contractor upon request. By displaying the findings on a tag attached to the access point of the truck it will maximise the visibility to all potential users and provide peace of mind that the days’ relevant checks have been completed before they start operations. If faults are found during the pre-op walkround then the status can be updated to show a “DO NOT USE” message, effectively quarantining the truck until repairs have been completed.
Telehandler Inspection Books - 25 Checklists
The continuing development of telehandlers (telescopic materials handlers) in terms of capacity and ..
£6.20
Telehandler Inspections - Weekly Checklist Kit
The continuing development of telehandlers (telescopic materials handlers) in terms of capacity and ..
£37.10
Telehandler Inspections - Daily Checklist Kit
The continuing development of telehandlers (telescopic materials handlers) in terms of capacity and ..
£109.50
Inspection Information Station
The information station will provide your workplace with the ideal central location to store inspect..
£233.20
Inspection Wallet and Pen
A handy wallet that not only provides additional protection from the elements but also gives inspect..
£6.20
Weather Resistant Inspection Holder
These industrial strength pockets have a press seal fastening to keep important documents clean and ..
£6.31
Inspection Book Dispenser
Allow the storage of checklists in a central location for quick and easy access to important inspect..
£13.25